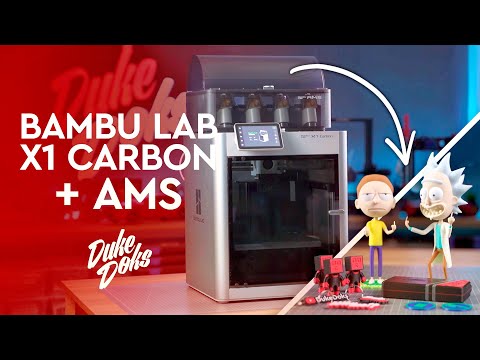
🌈 Mi experiencia con la BAMBU LAB X1 Carbon / Review / ¿Merece la pena?
Hello people, I have been testing this printer for a few months and in this video I am going to tell you all about my experience with it. Today I show you the Bambu Lab X1 Carbon with the AMS system. Let’s start at the beginning, when I received it, the first thing of all is to start it. It comes super well packaged and most importantly of all, practically completely assembled. Furthermore, the version that I received comes with the AMS module, or in other words, the multi-material module and some spools of filament to start testing it. But
first you have to remove all the protections it has. In this box it brings us the screen, glue for the bed, some spare parts, rear coil support , a complete spare fuser, cables, warranties and some keys for assembly. To start it up, the first thing is to remove the AMS from inside the printer, it is very well anchored with some screws that we will have to remove. The same piece that holds the AMS also holds the bed and other moving parts, this is just to hold everything in place for transport. We’ll remove it too. Now
we will put the screen, it is the only part that we will need to mount on the printer to start using it. We
PLA or they also call it a cold bed and another for more rough technical materials. We will also find two spare parts for the PLA part, it has a feel similar to that of PEI sheets. Now let’s go with the AMS. It has several pieces of Teflon tube for installation and spare parts and some compartments with silica bags to keep the filaments free of moisture. We will only have to place it on top or next to the printer, and connect the Teflon and cables as indicated in the instructions. And that’s it, in just a few
minutes we have it ready, the truth is that it is super pretty. The AMS reminds me of some kind of car engine. At first glance you can see that it is a very well built machine and gives a feeling of quality. But hey, the important thing is not that it is pretty but that it prints well. Let’s try it, the machine came with these filaments too. Support PLA, a basic PLA and a PLA with carbon fiber. Let’s start with the PLA. But not before telling you something about JLCPCB, which is the sponsor of this video.
They have had a 3D printing service for a long time, among other things. But this time they wanted me to show you on the one hand the 3D printing in transparent resin and on the other the metal printing. To order pieces you just have to go to their website, upload the STL files and in a few seconds you will know the price of your piece. You have many different 3D printing technologies and different materials to choose from. You just have to indicate what best suits your project and in a few days you will have a
package similar to this one in your home. The transparent resin is SLA printing, I have ordered my designs of the Rick and Morty characters and this is how they turned out. The quality is brutal. My idea was to paint them but the truth is that it makes me sad, they have their vibe just like that. This resin is great for pieces that we need to be transparent. A vase, the headlights of a radio-controlled car, I don’t know, anything. And on the other hand we have the prints in SLM, that is, metal. I had already shown
you this in other videos, a long time ago I ordered the reducer gears for the Cramer, one of my radio control projects, and they worked super well. So this time I ordered the gears for the differential case, both the ring gear and the small pinion. This technology is somewhat more expensive but we must keep in mind that in the end we are creating a fully functional metal piece. Don’t hesitate to take a look, remember that you can see the price of the piece just by uploading it, without having to order anything. They also have a
discount for new users until end of the year and design contest with various prizes such as discounts on their services and cash prizes. On their website you have all the conditions. If you are interested I leave you a link in the description. Thanks to JLCPCB for sponsoring this video, and now let’s move on. To test the machine we are going to start with the basic PLA. We just have to place it in one of the holes, insert the tip of the filament and the printer itself will load and recognize which filament it is. The Bambu
Lab spools have an NFC chip with the filament information so the printer recognizes it and knows at all times the settings to use with that material. It only purges the old filament and leaves the new one ready to print. In the machine’s memory we will already find several test files, so we are going to start with the benchy, which as it says here does it in 24 minutes. The speed this machine reaches is crazy, I have been using it for quite some time now and at normal speeds it is about 3 times faster than the
typical printers I was used to using Ender 3, Artillery X2, etc. and you are already seeing the quality. We see a change at the base, like it is brighter below, I guess it has to do with speed. Many materials are brighter or more matte depending on the temperature or speed at which we print them. On the other hand, we see on the bed that it also makes these lines, this is used by the lidar sensor on the cart to scan them and calibrate the flow of material. Of course, we can use filaments from other brands.
Only the machine won’t recognize them. We will have to indicate by hand what type of filament it is. We can even tell you the color. This is useful to recognize it on the laminator easily. Then, both from the laminator and in the gcode we can choose which AMS bay to use, although it has not allowed me to use the files that the machine already had, but then to others that I have prepared it has. In this case I had to change the filament to the first hole in the AMS. But as I said, it won’t
happen with the gcodes that we prepare. The next thing I have tried is PETG. I used it taking advantage of the fact that I had to make these letters, I also activated the ironing of the top layer and the truth is that the finish is brutal. And to finish with the most common materials, I have tried TPU. The only thing is that we cannot use TPU in the AMS, so we will have to place the coil support, disconnect the Teflon tube and insert the filament there. This is how we would use the machine if we
bought it without the multi-material system. TPU is the only material with which any impression has failed. I have tried disabling retractions and it worked. Perhaps it would be good to have adjusted the extruder pressure but I think it is not possible on this machine, so we will not be able to print TPUs that are too soft. But you see, the quality is very good, there is some thread due to having deactivated the retractions but it is normal, and the speed, although it drops a little because it is TPU, is still much faster than what we
are used to. To finish off the Cramer wheels, I have also printed the rims and here they are, ready to mount. But hey, we already know very well that this machine can handle any typical material that we use in any machine. But this printer has a hardened steel nozzle and goes up to 300 degrees, which means we can print things like carbon fiber materials. That ‘s why it includes a sample. So I’m going to print a Cramer differential in Carbon Fiber PLA and in the process I’ll take the opportunity to see how this material behaves
in the car. I have also tried ABS, it is a material that I do not usually print since it is advisable to do so in closed printers and practically none had passed through my hands, but on this machine it has been very easy. I have printed another spread on this material but I have also done bigger things. While printing these pieces, which by the way, are part of the next project, warping has appeared. It’s a problem that many people have reported and I wanted to check it out. This is when the pieces curve when they
cool and come off the corners, it happens a lot with ABS printing large pieces. On this occasion it has not come off but the force has managed to detach the magnet strap from the bed. Surely the strap is too thin or the magnet on the base is not very powerful. But removing this problem with warping, the truth is that it is a joy to be able to use so many materials. In addition to PLA, PETG, TPU, PLA with carbon fiber and ABS, I have also had time to try others such as PETG with carbon fiber,
Polycarbonate, and other technical materials. And as I say, a joy. Ok, we have already done quite a few tests with different materials, let’s now try different colors. These are some tests that I have taken from the gcodes that the printer had, they were perfect, but let’s try a real case. I’m going to color print my Rick and Morty designs. For this, the people at Smart Materials have sent me, in addition to this cool t-shirt, all the PLA colors that are needed. These for Rick and these for Morty. Bambu Lab recommends not using soft or cardboard
reels in the AMS. Or alternatively use reel adapters. But I think the cardboard of these coils is quite hard so let’s try it. We go to the Bambu Lab laminator and paint the piece according to the colors we want. I’m going to start with Morty’s head. This machine accepts up to 16 different materials, or in other words, 4 AMS. But since I only have one, I can only use 4, which is not bad either. I configure the 4 colors that I have put in the machine, being very careful that they are in the same order.
And with the painting tool I color the piece. If your design has very marked edges it will be very easy with the paint can, in this case I had to go over it a little with the normal brush. Well, simply with this, the laminator now knows how to prepare the gcode, and it also places a purge tower. With this we are ready to print. This is the first test, right now you are going to see how amazing it is. But of course, like everything, multi-material printing has its little things that we must take into account
for this and all similar multi-material systems. The first thing is to optimize as much as possible, what I mean by this, the more colors we use and the more material changes there are during printing, the more time and material we waste. And each material change takes about 1:30, it expels one of these balls and also prints a little on the purge tower. Many times the change of material will take longer than the printing of the layer itself. For example, Morty’s face alone goes from just under an hour to print in one color to almost 6
and a half hours to print in 4 colors. So far everything is logical, but look, in this case I have printed the two parts of Morty’s head. It is true that this way we save material and time because we only have one purge tower and some color changes are shared between the two pieces. But without a doubt, what saves the most is printing the same piece as many times as we can. Of course, this is only in case we want to make several identical figures. A clear example is that this print takes more or less
the same time to finish as this one. In this one we have this purge tower and this waste material, and in this one you are. Let’s print 1 figure or 7 of the same, the color changes will be the same and the purge towers will be the same. Another way to optimize is to adjust the amount of purge it does on each color change with this parameter. The more we lower it, the less it will purge, so we waste less material but we run the risk of not purging enough and the colors not coming out
as clean. It is clear that this depends a lot on the case, but if we want to optimize time and material as much as possible, we will have to pay close attention to these things. In conclusion, I can say that the AMS works very well, the colors come out super clean and I have had zero jams. But these types of systems, both AMS and similar, where we have a single fuser for all materials, a lot of time and material is wasted simply by having to purge one material with the next. Of course, you are already
seeing the results. Brutal. These are some more prints I have made with the machine. This is a case with screwdriver that my colleague Filaworks designed for me. I have also released it in various colors. It is prepared to put magnets inside, pausing the printing so that the box remains closed later. The truth is that the design is amazing, you can also download it without my logo. I leave you links to both this design and all those that appear in this video in the description. Another thing that becomes super simple is printing keychains. Quite a while
ago I invented a method to be able to print in various colors with a normal Ender 3 style printer, I leave you the video I made here. But with the Bambú and the AMS everything is now automatic. In all the time I have been using it, it has failed me on rare occasions, if not practically never. To conclude, I would like to summarize both the things that I liked and the things that I didn’t like so much. Because yes, there are also things that could be improved. Let’s start with the good things. We are facing
a brand that, despite being relatively new, we see has entered the market very strongly. Due to both the construction quality of its machines, as well as the speed and printing quality. Since behind it are engineers from the well-known drone brand Dji. In this case we have seen the X1 Carbon, which today is the top of the range sold by the brand and that is why it has all the extras. And this is the first positive point, it carries practically everything, everything that a 3D printer can carry. Camera, lidar sensor, active carbon filter, hardened steel nozzle,
temperature sensors even in the cabin, etc. Then, we have a multitude of features that promote printing speed and quality . Like a Y axis with carbon bars to reduce weight and inertia, a huge layer cooling fan that supports the one carrying the car, direct extrusion, it is a Core XY system, it has a super rigid structure. Then it is also able to identify if the first layer is good before continuing with printing or even has what they call spaghetti detection, that if the piece comes off and starts printing in the air, the machine recognizes it
and pauses the printing. impression. And things that may not be so necessary but that help the user experience, such as the internal camera to monitor the print, with which we can even make timelapses. Or the touch screen , which is a joy to be able to touch parameters, launch prints, configure filaments and so on. And then we also have the software part, it is great to use the machine from the Bambú Studio and the mobile app, although perhaps I have used the latter less, it has allowed me to monitor the machine when I have been
away from home. And finally, what I liked the most is how automatic it is. You don’t have to do absolutely anything. The machine does everything. The printing profiles that the software has are very good, everything is calibrated automatically, and the machine guides you very well and gives you warnings in case you are missing or have to do something. I sincerely believe that a person with no idea about 3D printing would be able to make a perfect piece. Maybe you’re thinking, my goodness, this printer is perfect. But the truth is no. It has many good things,
but it has others that I didn’t like. The first thing is the noise and vibrations it makes, it is impossible to have it next to you printing while you work if you don’t want to go crazy. But I guess it’s normal because of the speed at which it prints. To print quickly, you also have to cool the filament quickly, and the large fan it incorporates draws a lot of air flow, and this makes noise. The printer has a silent mode , but what this does is lower the printing speed, yes, it makes less noise, but
I don’t see the point in buying a printer like this and limiting it so that it doesn’t bother you. Another detail that I don’t like is the waste of the printing area. The area itself is not bad, we have a 256mm cube of printing area side. But what happens, the machine needs a little space to make its calibrations. Up ahead there is a corner that we cannot use and if we activate the flow calibration it makes these lines to calibrate. If we are also printing in multicolor, we need to put a purge tower somewhere. But
hey, a price to pay for all the automatic calibrations it does. On the other hand, there is the brand’s own laminator, the Bambú Studio. It works great, and for 99% of the cases it works perfectly. But perhaps advanced users may miss some parameters. For this there are other alternatives such as Orcaslicer. Then we have the issue of warping, as I told you before, it has only happened to me with ABS pieces that occupy the entire surface of the bed. But I think a stiffer strap or a more powerful magnet would solve this. Another thing to
mention is the waste of material. As I told you before, it is clear that it is something that is linked to this type of multi-material systems. But we will have to make an effort to optimize the printing if we do not want to waste more material than the part itself to be printed. On the other hand, if you are one of those who likes to tinker with machines, I think this is not for you. The modifications that can be made to this printer are rather few, in addition, you can only purchase spare parts on their
website. Although copies are already appearing on Aliexpress and other sites. Of course, for the price of an original compared to a clone, I think the clone is not worth it. The last negative is the price, but don’t get me wrong. It is a machine with a high price, yes, but I don’t think it’s worth it at all. For all the extras, for how it works, for the quality in all aspects, I think it is more than justified. And if you prefer to pay less, there are shorter versions of this machine that print just as well
and just as fast. Like the P1P or the P1S, some features are simply limited. And to finish with this video, who do I see this printer for? Well, mainly I see it as perfect for work environments. If you have a small business and you order keychains, earrings, figures, pieces in various colors, it is perfect. Also, if you need to do prototyping and the printing area is enough for you, you will have pieces with enough precision and at high speed and the possibility of using technical materials. It is a machine that works well and for a
business it is an easily amortizable investment. And as for personal use, if you are willing to pay the price, of course that too. It’s a fantastic machine and I totally recommend it. And just for today, tell me what you think of this machine, leave me a like if you liked the video, subscribe if you don’t and I’ll see you in the next video.